Fire Fighting Installation
Fire hazards are hazards caused by the potential threat and degree of exposure to radiant fire, starting from the beginning of the fire to the spread of fire, the spread of smoke and gas caused. Fire is the unwanted presence of fire. For the workforce, a building fire is a misery and a catastrophe, especially for those affected by the fire and has the possibility of impacting up to job loss, physical disability, trauma, and even loss of life. As for the building itself, it will be able to cause many losses, such as loss of important documents, damage to property and cessation of operational processes. Fire is one of the most common accidents. In addition to causing casualties and material losses, fires can also damage the environment and health problems caused by the smoke of the fire.
Because fire is a disaster that often occurs, it is necessary to have a system that can extinguish fires in a building or factory, in order to minimize the impact of the fire. However, the fire fighting process often fails.
Factors that cause failure and obstacles in fighting fires are due to inadequate fire protection equipment, unprepared human resources, or other obstacles. The existence of adequate fire protection will greatly assist the fire fighting process. So that it can minimize the losses obtained in the event of a fire. Existing human resources can also help to avoid fire hazards that occur.
Based on the problems that have been raised above, it is necessary to conduct a test check in accordance with the applicable statutory standards, so that if a fire occurs, the impact and losses received can be minimized.

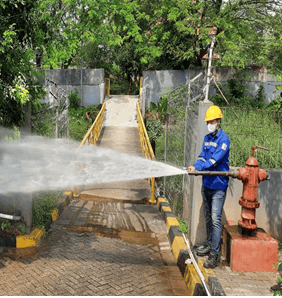
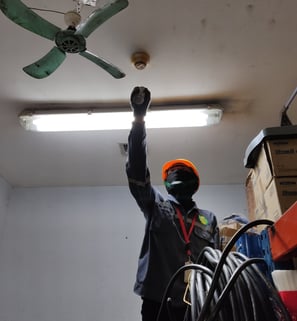
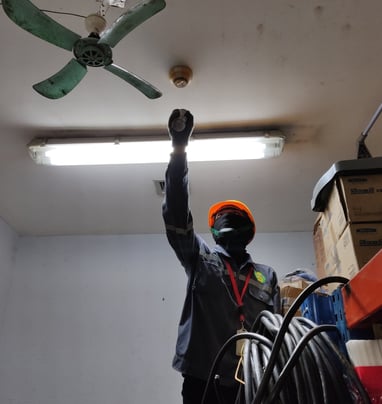
FIRE PROTECTION INSTALLATION TEST CONDITIONS
Newly installed Fire Protection Installations must undergo inspection and testing witnessed by authorized parties. Then the inspection and testing is repeated every year (annual inspection and testing).
The test check should be carried out jointly by two technicians, a competent and experienced person (AK3 Fire Fighting) and an assistant (Fire Technician Class DC). It is recommended that the building management be involved in the inspection from start to finish. Notes: Inspection and testing procedures may differ between service companies (PJK3) and manufacturers. i.e. the sequence of inspection and the criteria or limitations recommended among manufacturers.
Preparation for the inspection is divided into two parts, namely: a) Studying the technical specification document of fire protection installation design and layout to compare with Permenaker No. 2 of 1983. If there is any deviation, it should be noted and commented to be a concern. b) Putting up inspection signs on the door / fence so that public people do not interfere with the work of the inspection technician.
Both inspection/test technicians should wear safety helmets, safety shoes (non-slip soles). They should be prepared with checklists or forms, pocket-style battery flashlights, tools as necessary, and measuring instruments.
Both technicians must be aware or understand the Fire Installation Layout as a precautionary measure for possible incidents. If necessary, LOTO (lockout and tagout) should be installed during inspections carried out in the pump room to avoid accidents.
The annual retest check should pay more attention to the parts that work heavily, for the possibility of burning and damage.
Test inspection work is carried out by an expert and assisted by a technician, because many equipment are time-consuming to inspect one by one. Therefore, an inspector should be assisted by a competent technician, so that the duration of the inspection is only one hour or a maximum of two hours per system. Then another day is needed to prepare the report and discuss it with the building management.
TEST CHECKLIST
Includes data of the Fire Protection Installation, administrative requirements and the source of materials and standards used. Also events experienced by past installation networks, such as: demolition relocation/reinstallation with its irregularities.
Technical requirements and findings during the inspection and recommendations if necessary, and opinions/evaluations and/or conclusions/decisions.
TEST RESULT
Serviceability
Serviceability with certain conditions (replace components or need repairs)
Not usable at all
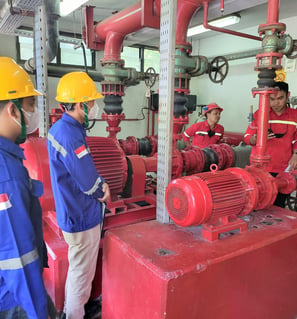
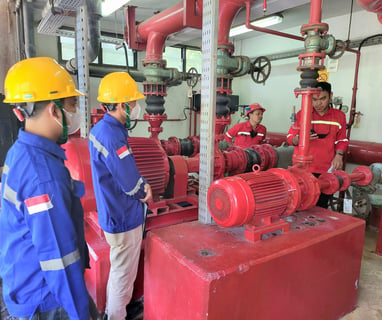